The manufacture of parchment
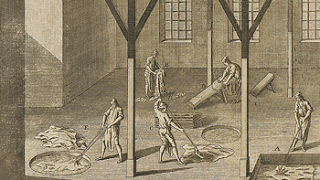
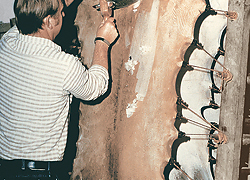
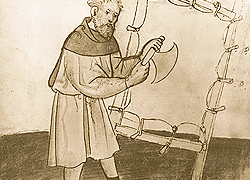
Below are the main procedures for the classical manufacture of parchment listed in the order they are to be executed.
- After skinning and before making the parchment, the raw skin should be temporarily conserved. The raw skin is preserved in a mixture of salts, preferably cooled, in order to prevent it spoiling biologically. In addition to salting, salting/drying and freezing are also used. It is important that the skins be carefully drained of blood. Any blood residue (iron salt in the blood) that is left in the veins may significantly damage the subsequent preservation of the parchment. Such damage is clearly identifiable on historical parchment.
- The next step in the manufacture of parchment is to soak the skinned raw skins in clean cold water for about 48 hours. This procedure helps to more effectively wash the blood, mucus, salts and other non-collagen proteins (chemically unbound aluminum, globulins) out of the dampened skin. In order to clean the skin and prevent bacterial damage, this procedure should be conducted while constantly stirring and changing the water (or under running water). If the non-collagen proteins are not properly eliminated, the parchment will later become stiff and less elastic.
- The length of the next step is 8 to 16 days, depending on the temperature – the process takes longer in the cold. The skin is soaked in slaked lime in a weak water solution in a strong alkaline environment (pH=10–12). The skins are stirred from time to time to ensure the even distribution of the solution and to prevent the development of air bubbles that may prevent the solution reaching the skins, and later, hamper the removal of the hairs. Skins, the wool or hairs of which will be used thereafter, are processed as follows: the inner side of the skins is covered with a paste of sodium sulfide (Na2S) and lime, which breaks down the hair follicles by soaking through the skin. The coat was removed and skins placed in a limewater to soak.
Starting in the 19th century, sodium sulfide (Na2S) and enzymes started to be added to the lime solution process in order to make it more efficient and faster. The process did cause an acceleration, but the parchment that was produced was also stiffer and less elastic.
According to Jewish cultural traditions, at this stage, a fermented paste made of flour or bran was used and this produced an exceptionally high level of skin processing. This procedure broke down the epidermis and loosened the coat, detached the lipids and other non-collagen matter. In the strongly hydrolyzable process, the qualities of the collagen fibers also deteriorate to the weakening of the hydrogen bonds between the fiber bundles.
After the soaking, the chemical characteristics of the skin are almost 40% worse due to the hydrolyzing impact of the amino acids. Both the structural periodicity of the microfibrils (d) as when as the skin’s shrinkage temperature are reduced. If initially, the shrinkage temperature of the raw skin (Ts) is approximately 63º C, then it is reduced as the result of processing (Ts ca 50º – 60º C). This is a significant difference in comparison to leather tanning, in which case the leather properties improved, as compared to the raw skin, as the result of tanning. Tanning agents also make the skin more resistance to biological and chemical impact. - The epidermis, which the slaked lime has broken down, the loosened coat and subcutaneous tissue is removed. In order to do this, the skin, with the coat on top, is placed on an upright curved wooden board called the ‘beam’. The hairs are removed using a half-moon knife. The epidermis is also scrapped off. Thereafter the skin is turned over and the inner surface is cleaned, by removed the fat and the loose subcutaneous tissue with a sharp curved knife. Today, machines are used for this procedure.
The skin is thinned by double-sided scrapping and basically consists of the dermis area which contains over 90% collagen. Instead of scrapping, the skin can also be mechanically split. Splitting also enables the removal of the upper skin layer, i.e. the epidermis, (hair-split) or subcutaneous tissue (flesh-split). To obtain super thin vellum of uniform double-sided splitting was also used. Soaked lamb and goat skins could easily be split. Various tools were used for splitting. Today machines are used. - In the manufacture of parchment, the second soaking in a weak slaked lime and water solution is extremely important.
During this procedure the solution affects the characteristic orientation of the collagen fibers making it occur randomly in the volume of the skin. This state of the collagen fibers enables them to be reoriented in the course of the subsequent damp stretching process into layers that are parallel with the surface. In the course of this procedure, the mechanical properties of the skin deteriorate. Depending on the type and size of the skin, a suitable time must be chosen for the soaking. Keeping the skin in the solution for an excessive amount of time may damage the collagen fibers to the point that it is impossible to evenly stretch the skin. And therefore, it may not be possible to stretch the skin into high-quality parchment. When drying, calcium carbonate (CaCO3) is created by the carbon dioxide found in the air and the lime in the parchment. - The subsequent washing must remove even the slightest slaked lime residue, in order to ensure that the skin is not damaged in the future.
- Thereafter, the damp, thinned and washed skin is examined. If any holes appear, this are stitched together in order to facilitate the stretching on the frame, and prevent the holes enlarging or tears developing. The wet skin in stretched on a frame that is accessible from both sides. Small, smooth pebbles (today, also small balls of wet paper) are placed on the edges of the skin at small intervals. The skin is turned back and a cord is tied around the small knobs that develop. The other end of the cord is pushed through the holes on the frame with the help of a sharp wooden stick. Nails are not suitable for attaching the skin to the frame, because in the course of the drying and shrinkage of the skin, the nails may cause tears. Metal clamps may leave stains on the skin.
After the processing, the skin’s network of collagen fibers is oriented randomly During the stretching, some of the network breaks but, layer by layer, the remainder becomes parallelly oriented to the surface layer. - In the course of stretching and tightening the skin, the extraneous layers are scrapped off and the skin is burnished on both sides. And as the skin dries, the damp, constantly stretched skin is thinned as needed.
Various scrapping methods are used. When more burnishing was done on the underside of the dermis, and the dermis’s top layer, in which there were finer collagen fibers, was preserved, a stronger surface was obtained. A material with soft, velvety surface was produced if more of the top layer of the dermis was burnished, and the softer underside of the dermis with its coarser fibrous structure was preserved.
Physical damage could easily occur during the final stretching and scrapping. The most common damage included splits and holes, and attempts were often made to stitch them together.
On the parchment records dating back to the Middle Ages, the traces of various scrapping tools are often visible. A linear texture caused by the use of scrapers with jagged cutting edges is very common. - As the final finishing for the damp skin, it is rubbed with porous, volcanic pumice stone with a high sodium (Na) and silicon dioxide (SiO2) content. To lighten the surface, chalk powder, calcium carbonate (CaCO3), which contains various salts of magnesium (Mg) and calcium (Ca), are rubbed into the damp skin. To achieve an especially white and high-quality surface, when a paste-like mixture of egg whites, flour, milk and slaked lime was used. The final finishing varied by region and by era. Thus, for instance, in 14th-century Byzantium, a mixture of egg whites and linseed was used to lighten the surface.
At this stage, the skin was also tinted if necessary. In the 15th century, it was known how to tint parchment purple, indigo blue, green, and peach. ill 8
The skins stretched on frames were dried outdoors, while avoiding direct sunlight and the rapid movement of air, since temperature that was too high, and drying that was too rapid could worsen the quality of the parchment. - The properly dried parchment (with a residual water content of over 10%) was removed from the frame (cut out with a knife) and was ready to be used as writing material. If the parchment dried out too much, and the water content fell to less than 10%, the skin would become brittle over time and start to peel off layer by layer (Damage C 6.7).
In addition to moisture, the finished parchment also contains calcium (1.6-2%). This calcium content helps make the parchment flexible and transparent. Thus, parchment with lower calcium content (ca 0.5%) is considerably stiffer (Vnouček, J. jt. Care and Conservation of Manuscripts 13, Proceedings of the 13 seminar, Copenhagen, 2011, pp.235–266).
The classical procedures for manufacturing parchment are time-consuming processes that take place in warm and damp environments, and which can already chemically and biologically damage the skin during the manufacturing.
If we know how to differentiate the damage caused to parchment during its manufacture from other damage, it is much easier to analyze the risk factors that impact the preservation of the parchment and predict the parchment’s stability.
In addition to the tradition parchment, which was used as a writing material, a slightly different kind of parchment was also produced – goldbeater’s parchment, which was an important tool for the makers of gold leaf. This type of parchment was made from the caecum of calves, 40 to 80 cm in length. Short treatments using slaked lime were used to produce it. The caecum was elastic and stretchable. And it could be made into a very thin (0.05–0.01 mm, elastic, strong and long-lasting parchment.
In addition, transparent parchment was also produced. To achieve this, the super-thin skin that was created at the end of the vellum manufacturing process was treated with a linseed oil, fish glue and water solution, or with rotten egg whites. Transparent parchment was used to decorate and copy manuscripts, and to produce material that would let in the light from windows.
In summary, when identifying damage, it is important to know the following about the manufacture of the parchment
- Knowing the specifics of how the parchment was produced makes it easier to analyze the causes of the damage.
- It is important to know that the mastery employed in manufacturing the parchment is an important factor impacting its durability.
- Even centuries later, the small mistakes made in the preparatory procedures are reflected in the properties of historical parchments.
- When analyzing the damage and state of parchment, it is useful to know that significant damage to historical parchment has often occurred during the manufacture of the parchment.